When swapping to a modern TREMEC manual transmission with overdrive, an often overlooked consideration is the driveshaft and driveshaft speeds. Yes, that means we have to talk science and that pesky thing called physics. Bear with us and we’ll simplify the equation of selecting the right driveshaft to make your TREMEC transmission installation smooth and trouble free.
A common mistake is thinking driveshaft speed is the same engine RPM. With an old 2- or 3-speed automatic transmission or a 3- or 4-speed manual, driveshaft speed does match engine RPM. But that’s not true with an overdrive transmission. When the transmission is in Overdrive gear the driveshaft is turning faster than the engine by a factor determined by the Overdrive gear ratio. With some TREMEC Magnum 6-speed transmissions equipped with a 0.5:1 Sixth Gear ratio, the driveshaft will turn twice as fast as the engine RPM. Not planning for this can lead to highway speed vibrations, damage to the transmission and possibly more.
The main factor to look at is the specific driveshaft’s critical speed. This is the RPM where the shaft will be stressed to the point of bending or whipping. When this happens the driveshaft will break and start whipping around destroying anything in its path, especially the transmission tunnel. Shrapnel can be sent into the vehicle’s interior and cause serious injury or death. A driveshaft’s critical speed is determined by the material it is from (steel, aluminum or carbon fiber) diameter and length.
You might be thinking, “my engine doesn’t make that much power; this shouldn’t be a problem,” but this issue is caused by driveshaft speed, not power. A lower horsepower engine can still spin an old steel driveshaft past its critical speed when a modern overdrive-equipped transmission is installed. If you’re wondering what driveshaft speed your car or truck is turning, use this online driveshaft speed calculator from Driveline Services.
On older cars and trucks, stock steel driveshafts can hold up fine with stock transmissions having a top gear ratio of 1:1 because they won’t exceed their critical driveshaft speed. Throw in a modern manual transmission like the TREMEC TKX 5-speed and its Fifth gear overdrive or a Magnum 6-speed and the original driveshaft can easily be pushed past its limit. Upgrading to a new, modern aluminum or carbon-fiber driveshaft not only reduces the risk of driveshaft failure, it also frees up some extra horsepower because either of the modern driveshafts weighs significantly less than the stock steel driveshaft. Less rotating mass means less power needed to turn.
To talk more about driveshafts and specifically carbon fiber driveshafts, we visited Gulfcoast Driveshafts in Tampa, Florida. Owner Shane walked us though of the shop and explained the process of making driveshafts, the differences between carbon fiber and aluminum along with other aspects of the driveshaft-making process.
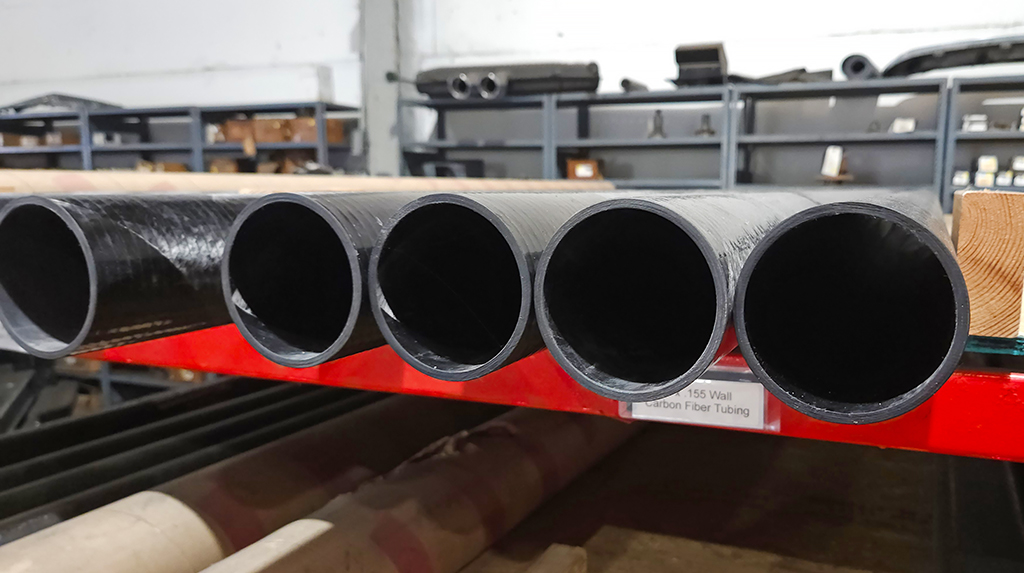
ABOVE: Carbon-fiber driveshafts start with a carbon-fiber tube. There are multiple diameters available to fit application needs. Carbon-fiber is the lightest of common driveshaft materials, providing the biggest reduction in reciprocating weight of the driveshaft, significantly increasing the driveshaft critical speed and reducing parasitic power loss.
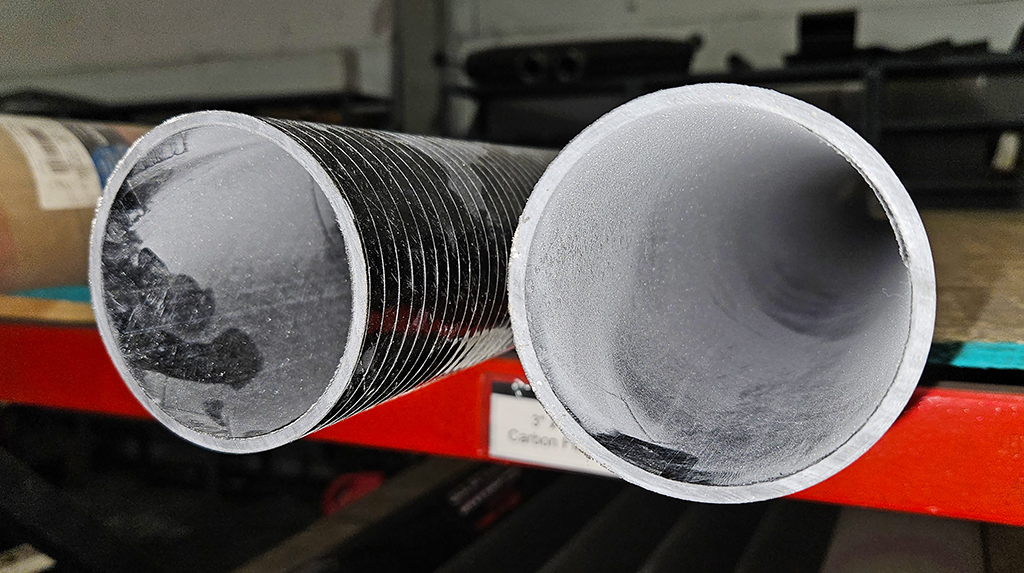
ABOVE: While carbon-fiber driveshaft failures are rare they do occasionally happen. Another advantage of a carbon-fiber shaft is that, if it fails, the shaft material breaks apart when it hits metal, doing minimal damage to a vehicle underbody.
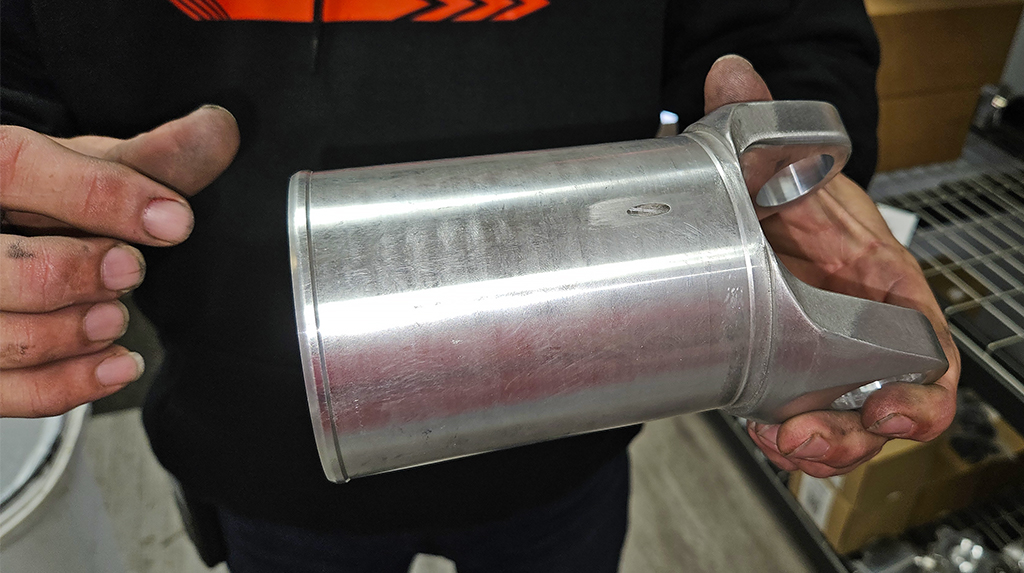
ABOVE: The ends of a carbon fiber shaft are machined aluminum pieces with yoke end. They are press fit into the carbon fiber shaft tube, with the machined lip helping to secure the end into the shaft.
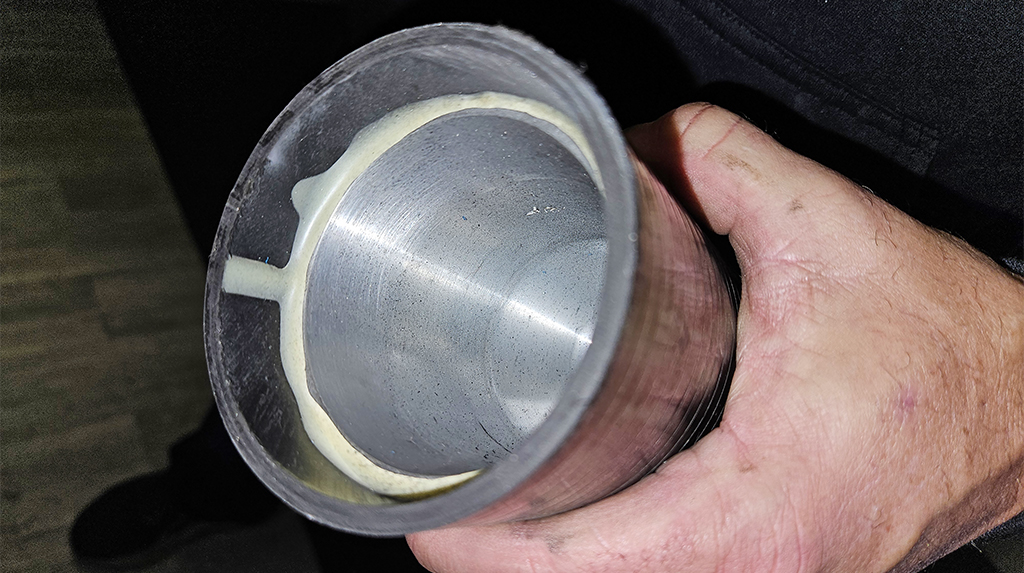
ABOVE: Specially formulated bonding adhesive is used to secure end piece yoke into the carbon fiber shaft tube. Thanks to the large surface area provided by the aluminum collar of the yoke piece, it bonds the end in place as solid as the yoke on an alloy shaft.
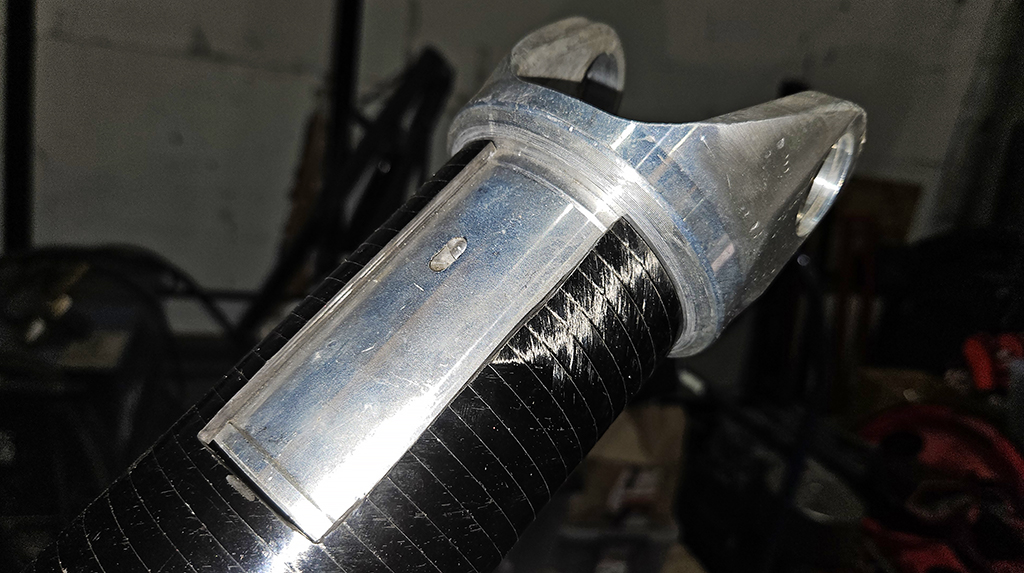
ABOVE: You can see here how far the yoke collar is pressed into the shaft tube. This large amount of surface area provides a secure and stable mount.

ABOVE: Once the bonding agent for the yoke ends has fully cured, the carbon-fiber driveshaft enters the next phases of construction. The shaft is secured in this fixture and twist tested. Enough torsional stress is applied to the shaft that the actual base of the test fixture will start to twist.

ABOVE: Both ends are monitored via laser for twist rate and deviation during torque test to verify the yoke ends are bonded in place properly. Gulfcoast Driveshaft is one of the few driveshaft companies that offers this type of torque testing using a special fixture built in-house. A carbon fiber driveshaft has a bit of torsional flex, so under load it will twist a small amount and rebound when the torsional force reduces. For drag cars in particular this helps with initial launch and can improve 60-foot times. For manual transmission drag cars this bit of rebound helps as the clutch is released and the engagement drags engine RPM down.
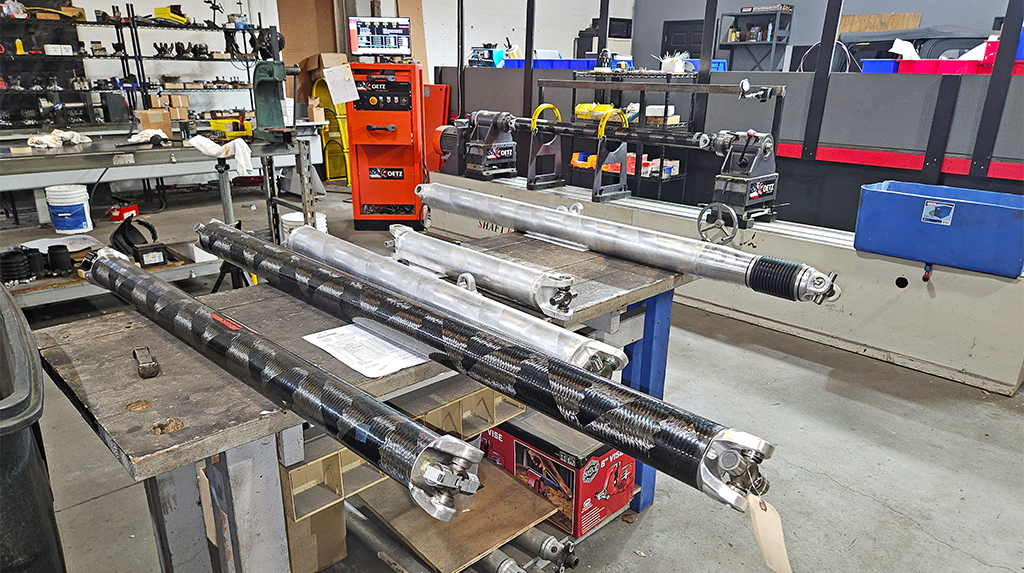
ABOVE: Gulfcoast Diveshaft also makes aluminum shafts for a variety of applications. For vintage cars and trucks where an OE steel driveshaft is being replaced, aluminum is an upgrade with a higher critical driveshaft speed but still not as high as the carbon-fiber shaft. With high-horsepower restomod style classics with a lot more horsepower and a transmission like the Magnum 6-speed with double overdrives, the critical driveshaft speed is a factor to be considered even for a street car. While a carbon-fiber driveshaft costs more than aluminum, that cost difference has to be weighed against performance benefits and safety.
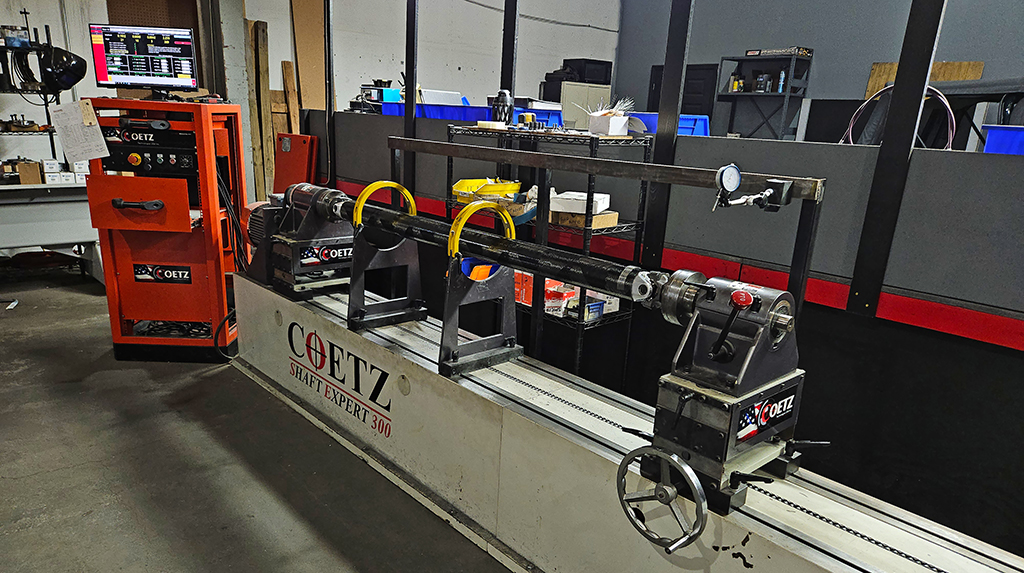
ABOVE: The final step of the process is balancing. Gulfcoast Driveshaft spin tests and balances their shafts at 2,500 and 5,500 RPM to make sure there are no harmonic issues at low and high driveshaft speed.
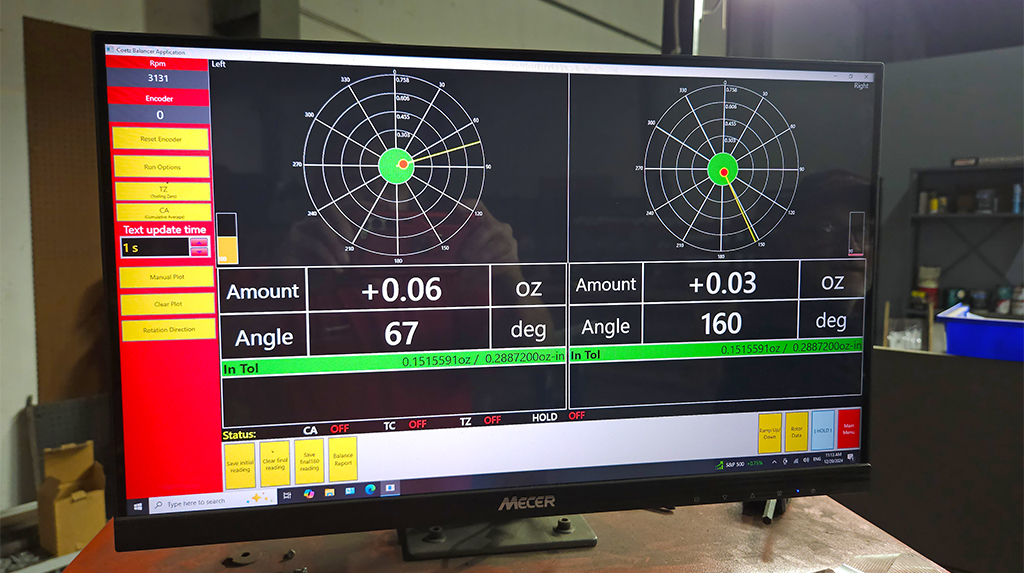
ABOVE: As the shaft is spun to test RPM, this screen will show how out of balance a shaft is and at what locations on the shaft counterweights need to be placed for proper balance. The shaft will be spun until it comes into balance.